Comment atteindre l’excellence opérationnelle ? (1/2)
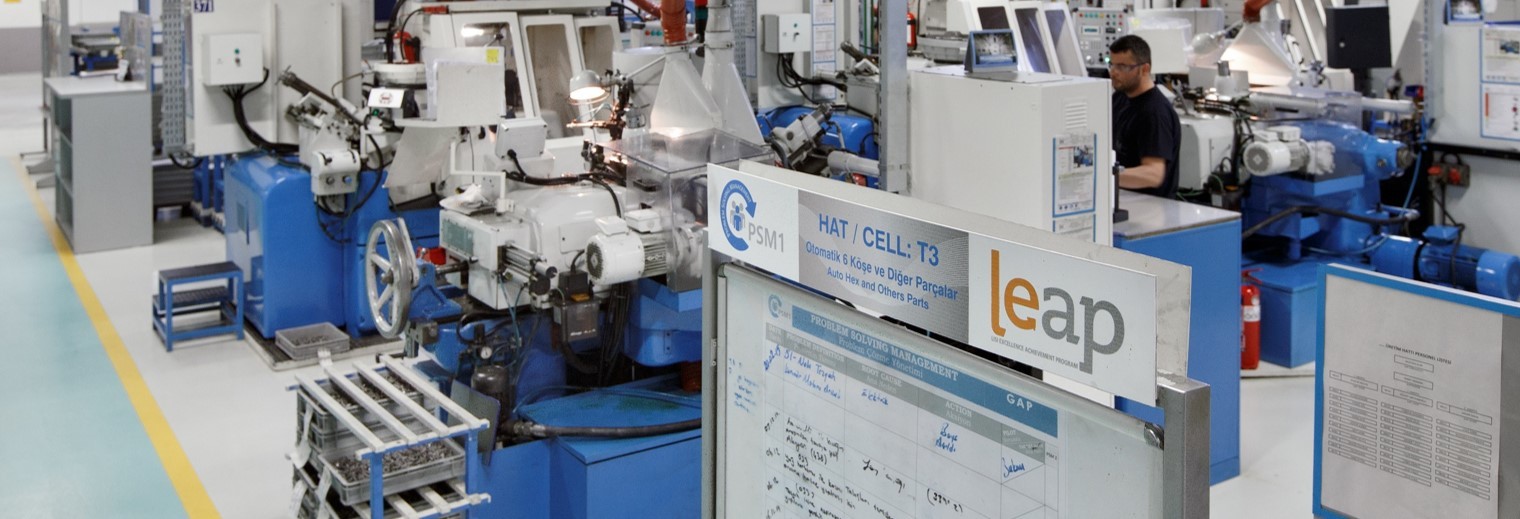
3 conseils pour ancrer la démarche et valider sa performance
La performance industrielle vise à répondre aux besoins des clients, tout en optimisant les ressources humaines et machines à disposition. Chez LISI, nous appelons cela la recherche de l’excellence opérationnelle.
La notion de performance industrielle a bien changé depuis l’époque de Ford et Taylor. Le client aujourd’hui n’est plus le même non plus. A l’époque, il s’agissait de produire une même et unique voiture avec une demande supérieure à l’offre. Leur unique préoccupation était de produire toujours plus, car ils étaient certains de trouver acheteur. Mais de nos jours, les besoins des clients sont variés et évoluent vite : ils exigent de nombreuses options, des personnalisations, et tout cela avec une grande rapidité de livraison. Les entreprises industrielles modernes doivent s’adapter.
La performance industrielle n’a de sens qu’à partir du moment où les attentes des clients sont comblées : qualité, délai, réactivité et service. La notion de réactivité est à ce titre un besoin récent et de plus en plus important.
Sur la base du Lean Manufacturing, notre performance industrielle s’exprime autour des 5 axes SQDCM :
- Sécurité
- Qualité
- Délai
- Coût
- Motivation (tellement importante et longtemps oubliée !)
Chez LISI, afin de suivre et d’évaluer notre performance industrielle, nous avons comme beaucoup d’autres industriels construits nos KPI (Key Performance Indicators) en lien avec ces 5 axes.
Vous trouverez dans la suite de cet article 6 conseils tirés de l’expérience du groupe LISI pour atteindre l’excellence opérationnelle.
1. PENSEZ GLOBAL ET AGISSEZ LOCAL
Comme dans toute démarche Lean Manufacturing, LISI a avant tout recherché l’optimisation globale, et pas seulement locale. Une sur-performance locale n’apporte pas nécessairement plus au global, notamment en raison de ce qu’on appelle « les goulets ». En effet, comme nous l’enseigne la théorie des contraintes : toute amélioration sur un moyen « non goulet » n’apporte pas d’amélioration globale à l’usine.
Je m’explique. Imaginons un schéma de production, où nos pièces passent d’abord par la machine A, puis par la machine B, puis par la machine C.
- On augmente la capacité de la machine A de manière conséquente.
- La machine B quant à elle maintient sa capacité de production. Elle reçoit de la machine A plus de pièces qu’elle ne peut en absorber, car sa propre capacité reste limitée.
- Par conséquent, en bout de chaîne, la machine C ne sort pas plus de pièces qu’avant. En effet, la machine B agit comme un « goulet ». Elle n’arrive pas à traiter le surplus de production de la machine A.
Dans cet exemple, une amélioration locale mal ciblée génère des effets pervers : elle crée du stock important entre A et B. L’accumulation des pièces augmentent les risques de sécurité liés à l’encombrement et à la manutention. Ce stock prend aussi de la place et augmente les coûts.
Conseil n°1 : Pensez toujours votre démarche de manière globale et agissez localement sur les contraintes (goulets).
2. LES DEUX AXES D’AMELIORATION DE LA PERFORMANCE
a- NE TOMBEZ PAS DANS LE PIEGE DE LA COURSE A LA CADENCE INSTANTANEE
En travaillant sur les cadences instantanées des machines, vous allez chercher à améliorer vos processus et le temps de cycle de votre fabrication. Travailler à l’amélioration des temps de cycle demande beaucoup de ressources et de connaissances des processus, ainsi que de longues et coûteuses séries d’essais et validations. Cela représente également un risque, car vous toucherez directement à votre façon de faire (processus) : la qualité pourrait être altérée.
C’est le levier préféré des ingénieurs et techniciens. Mais ce n’est pas celui qui rapporte le plus et le plus vite.
b- OPTIMISEZ L’UTILISATION DES RESSOURCES
Pour améliorer votre performance, vous pouvez vous inspirer des méthodes japonaises du Toyota Production System. Il ne s’agit ici pas seulement de réduire les temps de cycle, mais d’une véritable philosophie centrée sur la motivation et l’implication des collaborateurs qui vise à utiliser ses ressources 100% du temps disponible. Le Lean Manufacturingdéfinit 3 sources de non-productivité : éliminer ou diminuer une de ses sources générera automatiquement des bénéfices.
MUDA
Toute activité ou situation pendant laquelle le produit ne se voit pas ajouter de valeur.On classe les MUDA en 7 catégories de gaspillage : opérations inutiles, stocks, attentes, transports, mouvements, non qualité, surproduction. Une machine ou un homme qui attend représente un gaspillage de temps. Cherchez donc d’abord à utiliser les ressources à 100 %. La source de gains résidant dans la suppression des temps d’arrêt ou d’attente est nettement supérieur à celle de l’augmentation des temps de cycle. Et les actions sont souvent beaucoup plus simples à mettre en œuvre. Commencez donc par faire la chasse aux gaspillages.
MURI
On appelle MURI tout ce qui a pour conséquence un sentiment de démotivation des équipes : une surcharge de travail, un standard mal défini, des prises de décision qui requièrent une responsabilité qui n’est pas de son niveau, mais aussi le bridage de la créativité ou de l’autonomie. Supprimez ces irritants, et votre organisation s’en trouvera naturellement plus performante. Tous vos managers devraient être formés à ce concept.
MURA
Un MURA est une source de variabilité dans le système/processus. Or selon ce concept, chaque variabilité est source de désorganisation. Par exemple, vous produisez une pièce tantôt bonne, tantôt mauvaise. Votre client commande tantôt de grandes quantités, tantôt de petites quantités. Difficile de s’organiser et d’être efficace dans de telles conditions. Eliminez au maximum ces variations. En lissant votre production, vous serez plus performant. Pour réussir, veillez à bien maîtriser vos process (en utilisant l’outil 6 sigma par exemple), à la fiabilité des machines et des moyens de production, et lissez la demande des clients (flux tirés).
Vous pourrez trouver de nombreuses ressources sur Internet pour vous aider à identifier et supprimer les MUDA, MURI et MURA.
Conseil n°2 : L’amélioration des temps de cycle et l’optimisation des ressources sont complémentaires. Nous vous conseillons cependant de commencer par viser une utilisation des ressources à 100 %, au lieu de chercher tout de suite à augmenter les cadences instantanées. Mettez en exergue les MUDA, MURI et MURA et cherchez à les résoudre avant toute chose. ‘
3. DÉMARREZ PAR LES BASIQUES
LISI a commencé à structurer sa démarche Lean Manufacturing en 2013. En introduisant progressivement 3 programmes :
- E-HSE (Excellence HSE) focalisé sur les axes sécurité et environnement
- LEAP (LISI Excellence Achievement Program) pour répondre aux axes Sécurité, Qualité, Délai, Coût et Motivation
- COS (Controling Operating System) qu’on peut interpréter comme la conscience économique pour répondre à l’axe coût
Pour concevoir ces programmes, LISI s’est d’abord fait accompagner par la société HLP. Cette société de conseils en transformation industrielle nous a aidé à bâtir et personnaliser notre propre système de production appelé LEAP (LISI Excellence Achievement Program). Par la suite, le déploiement s’est intégralement appuyé sur nos ressources internes. Il était essentiel que les collaborateurs puissent s’approprier les méthodes et les outils. Appropriation sans laquelle, tout aurait risqué de s’effondrer au départ des consultants.
a- DÉVELOPPEZ LA CULTURE DU STANDARD
Nous avons commencé par développer la culture du standard. L’objectif est d’ouvrir l’esprit des collaborateurs sur la notion de standard et de chasse aux gaspillages en s’appuyant sur des outils simples (5S et SMED). Nous cherchons à chaque fois un standard pour améliorer nos process et éliminer les gaspillages. Pour la résolution des problèmes, nous nous appuyons sur l’outil 8D.
b- PROPOSEZ DES OUTILS DE MANAGEMENT
En parallèle, nous avons mis à disposition des outils de management simples et performants.
Plan stratégique A3 : Nous avons introduit les plans stratégiques A3 pour ne pas perdre de vue les actions entreprises sur le long terme. Le A3 est la cascade de la stratégie, du groupe jusqu’aux unités autonomes de production. C’est un outil qui oblige le management à s’interroger sur la façon d’atteindre les objectifs stratégiques et de s’astreindre à un suivi régulier au cours de l’année pour ne pas perdre le fil conducteur. C’est un processus top-down qui permet de décliner la stratégie à chaque niveau de l’entreprise.
PSM (Problem Solving Management) : Le PSM sert à la résolution des problématiques terrain à tous les niveaux de l’entreprise et au quotidien. C’est un processus bottom-up qui prend en compte et assigne toutes les problématiques du quotidien depuis les opérateurs jusqu’au directeur du groupe. Son objectif est que le problème soit traité au bon niveau, et donc par les bonnes personnes.
Il nous aura fallu presque 4 ans pour déployer ces systèmes sur notre quarantaine de sites et dans plus de 10 pays.
Conseil n°3 : commencez par les basiques. Introduisez d’abord la culture du standard et la chasse aux gaspillages avec des outils simples. Puis donnez aux managers des outils robustes pour piloter le quotidien et le long terme.